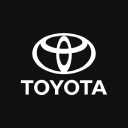
Karachi, 75020,
Pakistan
Toyota Indus Motors Technographics
Discover the latest software purchases and digital transformation initiatives being undertaken by Toyota Indus Motors and its business and technology executives. Each quarter our research team identifies on-prem and cloud applications that are being used by the 4000 Toyota Indus Motors employees from the public (Press Releases, Customer References, Testimonials, Case Studies and Success Stories) and proprietary sources.
During our research, we have identified that Toyota Indus Motors has purchased the following applications: Limestone Networks Cloud for Application Hosting and Computing Services in 2018, Microsoft 365 for Collaboration in 2017, WooCommerce for eCommerce in 2017 and the related IT decision-makers and key stakeholders.
Our database provides customer insight and contextual information on which enterprise applications and software systems Toyota Indus Motors is running and its propensity to invest more and deepen its relationship with Limestone Networks , IBM , Microsoft or identify new suppliers as part of their overall Digital and IT transformation projects to stay competitive, fend off threats from disruptive forces, or comply with internal mandates to improve overall enterprise efficiency.
We have been analyzing Toyota Indus Motors revenues, which have grown to $3.22 billion in 2024, plus its IT budget and roadmap, cloud software purchases, aggregating massive amounts of data points that form the basis of our forecast assumptions for Toyota Indus Motors intention to invest in emerging technologies such as AI, Machine Learning, IoT, Blockchain, Autonomous Database or in cloud-based ERP, HCM, CRM, EPM, Procurement or Treasury applications.
IaaS
Vendor |
Old Product |
New Product |
Category |
Market |
VAR/SI |
When |
Live |
---|---|---|---|---|---|---|---|
Limestone Networks | Legacy | Limestone Networks Cloud | Application Hosting and Computing Services | IaaS | n/a | 2018 | 2018 |
|
|
|
Application Hosting and Computing Services | IaaS |
|
2018 | 2018 |
|
|
|
Content Delivery Network | IaaS |
|
2020 | 2020 |
Collaboration
Vendor |
Old Product |
New Product |
Category |
Market |
VAR/SI |
When |
Live |
---|---|---|---|---|---|---|---|
Microsoft | Legacy | Microsoft 365 | Collaboration | Collaboration | n/a | 2017 | 2017 |
eCommerce
Vendor |
Old Product |
New Product |
Category |
Market |
VAR/SI |
When |
Live |
---|---|---|---|---|---|---|---|
Automattic | Legacy | WooCommerce | eCommerce | eCommerce | n/a | 2017 | 2017 |
ERP Financial Management
Vendor |
Old Product |
New Product |
Category |
Market |
VAR/SI |
When |
Live |
---|---|---|---|---|---|---|---|
|
|
|
ERP Financial | ERP Financial Management |
|
2018 | 2018 |
SCM
Vendor |
Old Product |
New Product |
Category |
Market |
VAR/SI |
When |
Live |
---|---|---|---|---|---|---|---|
|
|
|
Supply Chain Management | SCM |
|
2017 | 2017 |
First Name | Last Name | Title | Function | Department | Phone | |
---|---|---|---|---|---|---|
No data found |
Date | Company | Status | Vendor | Product | Category | Market |
---|---|---|---|---|---|---|
No data found |